What is Porosity in Welding: Best Practices for Avoiding Permeable Welds
What is Porosity in Welding: Best Practices for Avoiding Permeable Welds
Blog Article
The Science Behind Porosity: A Comprehensive Guide for Welders and Fabricators
Comprehending the intricate mechanisms behind porosity in welding is important for welders and makers striving for remarkable craftsmanship. From the composition of the base products to the details of the welding process itself, a wide range of variables conspire to either aggravate or alleviate the presence of porosity.
Comprehending Porosity in Welding
FIRST SENTENCE:
Assessment of porosity in welding reveals vital understandings right into the stability and quality of the weld joint. Porosity, characterized by the existence of dental caries or gaps within the weld metal, is a typical concern in welding processes. These voids, otherwise properly addressed, can endanger the structural honesty and mechanical homes of the weld, leading to prospective failings in the completed item.

To identify and evaluate porosity, non-destructive testing methods such as ultrasonic testing or X-ray examination are typically utilized. These methods permit the recognition of inner issues without compromising the stability of the weld. By examining the dimension, shape, and distribution of porosity within a weld, welders can make educated decisions to improve their welding procedures and achieve sounder weld joints.
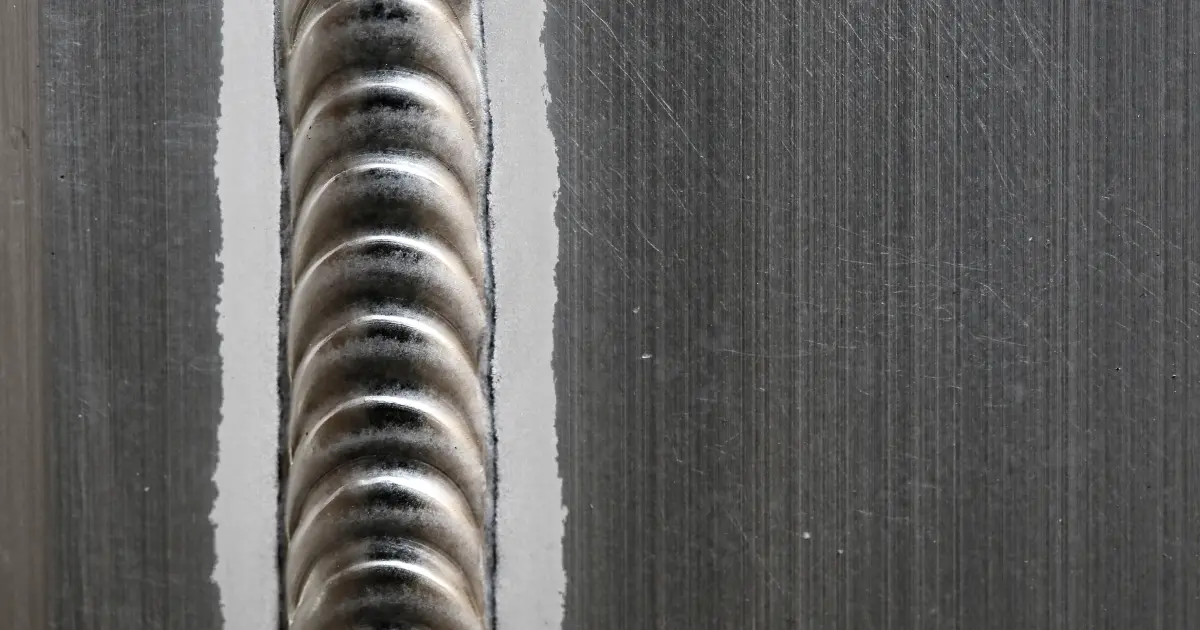
Aspects Influencing Porosity Formation
The event of porosity in welding is influenced by a myriad of elements, varying from gas shielding efficiency to the details of welding criterion settings. Welding specifications, including voltage, present, travel rate, and electrode type, likewise effect porosity development. The welding method used, such as gas steel arc welding (GMAW) or secured metal arc welding (SMAW), can affect porosity development due to variants in warmth circulation and gas insurance coverage - What is Porosity.
Effects of Porosity on Weld Quality
The visibility of porosity likewise deteriorates the weld's resistance to corrosion, as the entraped air or gases within the spaces can respond with the surrounding atmosphere, leading to deterioration over time. Furthermore, porosity can hinder the weld's capacity to stand up to pressure or effect, additional jeopardizing the overall quality and integrity of the bonded structure. In critical applications such as aerospace, automobile, or structural building and constructions, where safety and security and longevity are vital, the damaging results of porosity on weld quality can have extreme consequences, stressing the importance of minimizing porosity with proper welding strategies and procedures.
Methods to Minimize Porosity
In addition, utilizing the proper welding parameters, such as the proper voltage, current, and take a trip speed, is important in preventing porosity. Preserving a constant arc length and angle during welding also aids reduce the pop over to this site possibility of porosity.

In addition, selecting the best shielding gas and keeping proper gas flow prices are necessary in reducing porosity. Using the ideal welding method, such as back-stepping or using a weaving activity, can additionally assist distribute heat uniformly and reduce the opportunities of porosity formation. Finally, guaranteeing proper air flow in the welding setting have a peek at this website to get rid of any type of prospective sources of contamination is essential for accomplishing porosity-free welds. By implementing these techniques, welders can effectively decrease porosity and create top quality bonded joints.
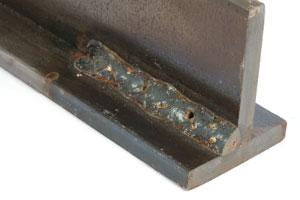
Advanced Solutions for Porosity Control
Applying advanced modern technologies and ingenious methods plays an essential duty in attaining premium control over porosity in welding processes. Furthermore, using innovative welding techniques such as pulsed MIG welding or customized ambience welding can additionally help reduce porosity problems.
An additional innovative solution entails using sophisticated welding devices. As an example, utilizing equipment with built-in attributes like waveform control and advanced source of power can improve weld top quality and reduce porosity risks. Furthermore, the application of automated welding systems with specific control over parameters can dramatically decrease porosity issues.
Furthermore, including innovative surveillance and examination innovations such as real-time X-ray imaging or automated ultrasonic testing can aid in finding porosity early in the welding process, enabling prompt rehabilitative browse around these guys activities. Overall, incorporating these advanced solutions can greatly boost porosity control and enhance the overall top quality of welded parts.
Conclusion
Finally, recognizing the scientific research behind porosity in welding is necessary for welders and makers to generate top notch welds. By identifying the aspects affecting porosity formation and applying methods to decrease it, welders can enhance the overall weld high quality. Advanced services for porosity control can better enhance the welding procedure and make sure a strong and reliable weld. It is essential for welders to constantly enlighten themselves on porosity and execute ideal practices to accomplish optimal outcomes.
Report this page